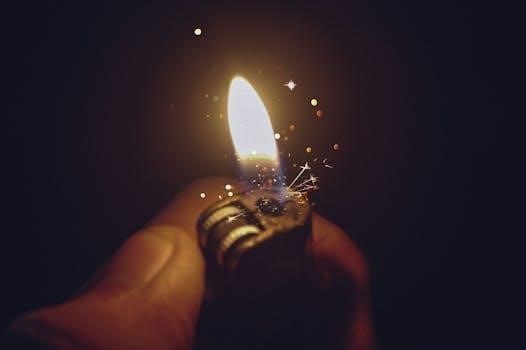
This document provides crucial safety tips for preventing hand and finger injuries. It emphasizes the importance of training and pre-use tool inspections. Regular toolbox talks should focus on safe work practices and foster group discussions regarding hand safety issues. These talks are essential for educating workers.
Importance of Hand Safety
Hand safety is paramount in any workplace, as hands are frequently exposed to various hazards. Protecting them from potential injuries is not just a matter of compliance; it’s a fundamental aspect of ensuring worker well-being and productivity. Ignoring hand safety can lead to severe consequences, including cuts, lacerations, fractures, burns, and even more debilitating injuries. These injuries can result in lost work time, reduced earning potential, and a decreased quality of life. Hand injuries are among the most common workplace incidents, making it essential to prioritize preventive measures. Moreover, a proactive approach to hand safety fosters a culture of care and responsibility among employees, highlighting that worker well-being is a top priority. This approach includes proper training on hand protection, the correct use of hand tools, and the importance of wearing appropriate gloves. By implementing robust hand safety protocols, employers can significantly reduce the risk of injuries and create a safer work environment. Regularly emphasizing the importance of hand safety through toolbox talks is critical in reinforcing these practices and ensuring that all workers are aware of the potential dangers and how to avoid them; Ultimately, hand safety is an investment in the health and productivity of the workforce.
OSHA Requirements for Hand Protection
OSHA mandates that employers provide appropriate hand protection for employees exposed to hazards that could cause hand injuries. These hazards include, but are not limited to, cuts, abrasions, punctures, chemical burns, thermal burns, and harmful temperature extremes. Employers are required to conduct a hazard assessment to identify potential risks and select the proper hand protection, ensuring that it fits properly and is appropriate for the specific task. OSHA’s regulations emphasize the importance of using the correct type of gloves and other protective equipment. In addition to providing the necessary protection, employers must also provide training on the correct use and maintenance of hand protection equipment. This training should include how to properly put on and remove gloves, when to replace damaged gloves, and the limitations of different types of gloves. Failure to comply with OSHA standards can result in citations, fines, and potentially, legal action. Furthermore, adhering to OSHA requirements is not just about compliance; it’s about creating a safe and healthy work environment for all employees. Regular toolbox talks and safety meetings should reinforce OSHA’s hand protection requirements and ensure that all employees understand their responsibilities in maintaining a safe workplace. By diligently following these guidelines, employers can minimize the risk of hand injuries and demonstrate a commitment to worker safety.
Common Hand Injury Hazards
Hand injuries are prevalent in many workplaces, stemming from a variety of hazards; Common risks include cuts and lacerations from sharp tools or materials, which can occur when handling knives, blades, or sheet metal. Puncture wounds are another significant concern, often caused by nails, splinters, or improperly handled sharp objects; Abrasions, resulting from friction against rough surfaces, can also lead to discomfort and potential infection. Chemical burns pose a severe threat, particularly in environments where workers handle corrosive substances without adequate protection; Thermal burns from hot surfaces or materials are equally dangerous. Additionally, exposure to extreme temperatures, both hot and cold, can lead to tissue damage and discomfort. Crushing injuries, frequently resulting from heavy machinery or equipment malfunctions, are often debilitating. Repetitive motion injuries, such as carpal tunnel syndrome, can develop over time due to prolonged use of hand tools or repetitive tasks. Furthermore, electrical hazards from working with energized equipment can cause severe burns and nerve damage. It’s essential to recognize these hazards and consistently apply safety precautions. Pre-use inspections of tools, proper training, and the appropriate use of personal protective equipment, such as gloves, are all essential in mitigating the risk of hand injuries. Regular safety meetings and toolbox talks should also address these hazards to foster a culture of safety awareness; By proactively identifying and addressing these risks, we can work to prevent common hand injuries in the workplace.
Pre-Use Tool Inspections
Prior to using any hand tool, a thorough inspection is crucial to ensure safe operation and prevent potential injuries. This inspection process should become a standard practice for all workers. Firstly, examine the tool for any signs of damage. Look for cracks, bends, or chips in the handle, head, or blade. A damaged tool can easily break during use, leading to serious injuries. Check for loose parts, such as screws, bolts, or rivets. Ensure that all connections are secure to prevent the tool from falling apart while in operation. For tools with cutting edges, inspect for sharpness. A dull blade requires more force, which increases the risk of slipping and causing cuts. Ensure that the cutting edge is properly sharpened or replaced as needed. If using power tools, check the power cord for fraying or damage to the insulation. A damaged cord can lead to electrical shock. Verify that the tool’s guards and safety devices are in place and functioning correctly. These are designed to protect the user from injury. Confirm that any moving parts, such as triggers, switches, and blades, operate smoothly without obstruction. Clean the tool of any dirt, debris, or grime, as this can affect its performance. Regular maintenance, including cleaning and lubrication, should also be performed periodically. By adhering to these pre-use inspection protocols, you can significantly reduce the risk of accidents and injuries.
Proper Use of Hand Tools
Using hand tools correctly is vital for preventing injuries and ensuring efficiency in any task. Firstly, always select the right tool for the job. Attempting to use the wrong tool can lead to damage to the tool, the material you’re working with, or even cause an injury to yourself. Ensure you have a firm grip on the tool, keeping your hand away from any cutting edges or moving parts. Maintain a stable stance and avoid overreaching or working in awkward positions that might cause a loss of balance or control. When using striking tools like hammers or mallets, strike squarely on the intended target, avoiding glancing blows that can cause the tool to slip. For cutting tools, always cut away from your body. This reduces the risk of cutting yourself if the tool slips. Use a secure work surface or clamping device to stabilize the material you are working on. This prevents unexpected movement that could lead to accidents. Apply even and controlled pressure. Never force a tool beyond its intended capacity. If a tool is not working as expected, stop and reassess the situation. Don’t try to force it. When using tools that require two hands, use both hands for better control and stability. Always keep your hands clear of any moving parts or pinch points. After completing the task, make sure to clean the tool and store it properly in its designated location.
Selecting Appropriate Gloves
Choosing the right gloves for the task at hand is crucial for hand protection and safety. Different jobs present different hazards, and therefore, require different types of gloves. For tasks involving sharp objects or abrasive materials, select gloves made from durable materials like leather or heavy-duty fabrics. These materials offer protection against cuts, punctures, and abrasions. For tasks that involve handling chemicals, choose chemical-resistant gloves made of materials like neoprene, nitrile, or PVC. Ensure the gloves you select are compatible with the specific chemicals you will be using. When working with electricity, wear insulated gloves that meet the required safety standards for the voltage involved. Make sure that the gloves are tested and certified for electrical protection. For tasks that require dexterity, like handling small parts, select gloves that provide a good fit and do not restrict movement. Lightweight gloves made of materials like cotton or nylon might be ideal for these tasks. Consider the fit of the gloves as well. Gloves that are too loose can impede your grip, while gloves that are too tight can cause discomfort and reduce dexterity. Always inspect your gloves before each use for any signs of damage, such as tears, punctures, or discoloration. Replace damaged gloves immediately. Also, ensure that the gloves are clean before using them. Dirty gloves can contaminate the work environment or cause skin irritation. Finally, always follow your company’s safety procedures and regulations regarding glove selection.
Electrical Hand Tool Safety
Working with electrical hand tools presents unique safety challenges that demand careful attention and adherence to safety protocols. Always start by ensuring that all electrical tools are properly grounded or double-insulated, protecting you from electrical shocks. Before use, meticulously inspect the tool’s cord, plug, and housing for any signs of damage, such as frays, cracks, or loose connections. Never use a tool with damaged parts. Avoid working with electrical tools in damp or wet conditions, as water can significantly increase the risk of electrical shock. If working in wet conditions is unavoidable, use only tools that are specifically rated for such environments. Always use a ground fault circuit interrupter (GFCI) when working with electrical tools in damp or wet conditions. Make sure to switch off the power source before changing bits, blades, or accessories on any electrical hand tool. Never carry a tool by its cord, and avoid pulling or yanking the cord when unplugging the tool from an outlet. When working near electrical sources, be sure to maintain a safe distance from live wires and equipment. Always use appropriate personal protective equipment (PPE), such as insulated gloves and safety glasses, when working with electrical tools. If you’re not comfortable working with electrical hand tools or do not have the proper training, always seek the guidance of a qualified professional. Regularly check the tool’s safety features are in good working order. It is better to be cautious than to take risks when working with electricity.
Regular Safety Meetings and Toolbox Talks
Consistent safety meetings and toolbox talks are crucial for maintaining a safe working environment and preventing hand injuries. These sessions should be conducted regularly, ideally at the start of each shift or on a weekly basis, to reinforce safety procedures and address any new or emerging hazards. The primary aim of these meetings is to educate workers on safe work practices, covering topics such as proper tool usage, hazard identification, and the importance of wearing appropriate personal protective equipment. Toolbox talks should be interactive, encouraging open discussions and allowing workers to share their experiences and concerns. This participatory approach helps foster a culture of safety where everyone feels responsible for their own well-being and the well-being of their colleagues. Regular safety meetings should also be used to review any recent incidents or near misses, identifying the root causes and implementing corrective actions to prevent future occurrences. These meetings should be a platform for continuous improvement, allowing the team to learn from past mistakes and refine their safety protocols. It is essential that all workers attend these meetings, and documentation should be kept to ensure accountability and track the effectiveness of the safety program. Remember that a proactive approach to safety, involving regular meetings and toolbox talks, is the most effective way to minimize risks and create a safe workplace for everyone involved. These sessions should be a priority for the company, as they demonstrate a commitment to the safety and well-being of the workforce.
Focus of Toolbox Talks
The primary focus of toolbox talks regarding hand safety should be on the prevention of hand and finger injuries through practical guidance and open discussion. These talks should emphasize the importance of identifying and mitigating potential hazards associated with hand tools and manual tasks. Key topics should include proper techniques for using specific tools, the appropriate selection of gloves and other protective equipment, and the risks associated with shortcuts or improper procedures. Discussions should also cover the significance of pre-use tool inspections to ensure that tools are in good working condition and free from defects that could lead to injury. Toolbox talks should provide workers with specific examples of common hand injuries and how they could be avoided, encouraging them to share their own experiences and insights. These sessions should aim to reinforce the message that safety is everyone’s responsibility, fostering a culture where workers feel comfortable speaking up about potential hazards and suggesting improvements. The goal is to move beyond a compliance-based mindset to one of proactive awareness and active participation in creating a safer work environment. Toolbox talks should not be a lecture but rather an interactive exchange of information, allowing workers to learn from each other and reinforce their understanding of safe work practices. By focusing on practical, real-world scenarios, these talks can be highly effective in reducing the risk of hand injuries in the workplace. Remember that the focus is on prevention and continuous improvement in the safety of the working environment.
Confidentiality in Safety Discussions
Maintaining confidentiality during safety discussions, particularly within toolbox talks, is paramount to creating a safe and trusting environment where workers feel comfortable sharing their experiences, concerns, and near-misses. When discussing incidents or potential safety issues, it is critical to focus on the facts of the situation and avoid assigning blame or making judgments about individuals. Workers need to know that they can speak openly without fear of reprisal or negative consequences. Confidentiality ensures that personal information remains private and is only shared with those who need to know to take corrective action. This can involve redacting names or any other identifying information that may be disclosed during these discussions. The goal is to learn from the experience, not to identify and punish individuals. Emphasize that the primary aim of these discussions is to improve safety protocols and prevent future accidents, not to seek out fault; Establish clear guidelines about how personal information will be handled during these safety talks, and be sure that everyone understands the importance of respecting these guidelines. It’s crucial to foster a culture of trust where employees are encouraged to report incidents and near-misses knowing that they will not be penalized for coming forward. By respecting confidentiality, organizations can promote open communication and a proactive approach to safety, fostering a safer work environment for everyone. This culture of trust and discretion is essential for the success of any safety program.
Prioritizing Worker Safety
Worker safety should always be the number one priority for every organization, and this principle must be ingrained in every aspect of operations, especially when dealing with hand safety. Implementing effective hand safety protocols is not just a regulatory requirement; it’s a moral obligation to ensure the well-being of all employees. This commitment begins with a clear and unequivocal message that safety is the company’s highest priority. Providing adequate training and education, readily available personal protective equipment (PPE), and conducting regular safety meetings and toolbox talks are essential steps. These efforts demonstrate the company’s dedication to creating a safe work environment. It’s crucial to actively involve workers in the development and implementation of safety programs. Their input and feedback are invaluable in identifying potential hazards and improving existing safety procedures. Regular reviews and updates of safety protocols, based on best practices and worker feedback, are also essential. Furthermore, ensuring that workers have the necessary tools and equipment in good working condition is a critical element of prioritizing their safety. Promptly addressing any safety concerns or hazards reported by employees is equally important. Prioritizing worker safety is not just about compliance; it’s about fostering a culture where every employee feels safe, respected, and valued. Ultimately, a strong commitment to safety reduces accidents, boosts morale, and contributes to a more productive and efficient workforce.